EXPLORING THE AIR SUSPENSION SYSTEM
In this article, Arnott explains how air suspension works
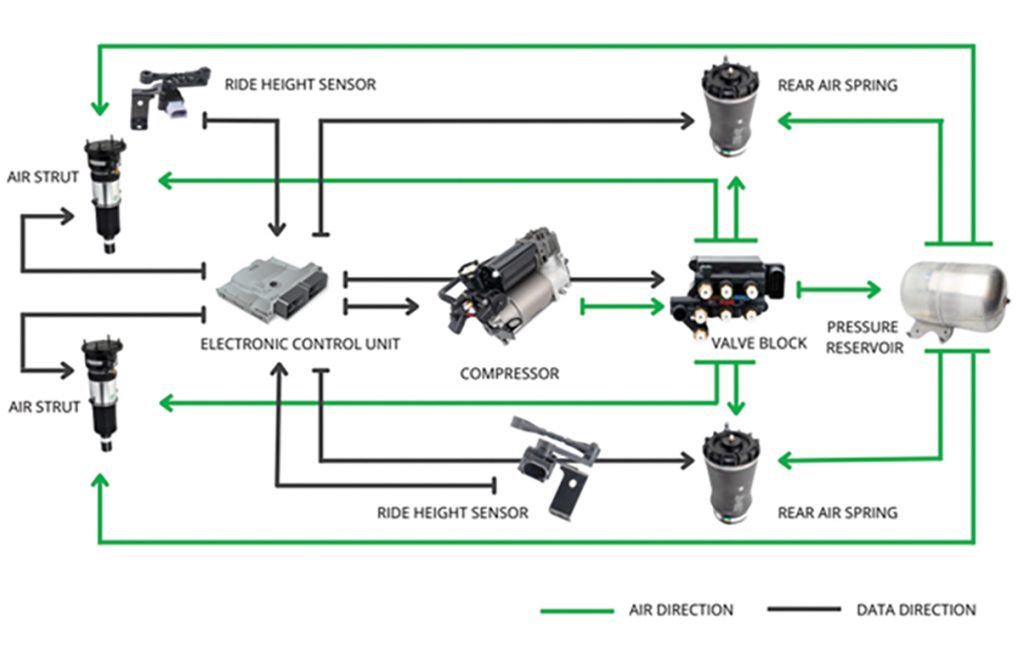
Arnott says air suspension systems have revolutionised the automotive industry by offering superior comfort, enhanced handling, and customisable adaptability.
Unlike traditional coil-spring suspensions, air-spring suspensions utilise pressurised air chambers to provide a smoother, more tailored ride.
The key components of air spring suspension include air struts and springs; the compressor; the valve block; the pressure reservoir; the Electronic Control Unit (ECU); and ride height sensors.
The struts, springs, and shock absorbers in an air suspension system function similarly to those in conventional coil suspension systems, but with one key difference: instead of coil springs, pressurised air springs bear the vehicle’s weight.
Shock absorbers work alongside the air springs to control damping and smooth out road impacts. Together, they help the vehicle maintain the right ride height, enhance suspension performance, and adjust seamlessly to different loads.
The air struts and/or air springs are at the core, paired with separate shock absorbers. In a full air suspension setup, each corner – both front and rear – is equipped with either an air strut or a combination of an air spring and shock absorber.
Each Arnott air spring features a multi-ply, cross-corded rubber design for durability and long-lasting performance.
Stainless steel crimping rings ensure an airtight seal between the rubber sleeve and the upper and lower mounting components.
While air springs are subject to wear and tear, they are designed to withstand extreme temperatures and resist constant exposure to dirt and road debris.
Air springs have an expected lifespan of six to 10 years, depending on usage and environmental conditions.
The compressor supplies and regulates the air pressure needed to maintain the air springs at the desired level.
Many compressors include an integrated dryer that absorbs moisture from the system. This moisture evaporates due to the heat generated by the compressor and is expelled into the atmosphere each time the pressure-release valve opens to release excess air pressure.
When height sensors detect that the vehicle has deviated from its preset height, the Electronic Control Unit (ECU) activates the compressor.
The compressed air flows through the valve block and air hoses to the air springs, adjusting the ride height as necessary.
In case the system has a pressure reservoir, the pressure normally comes directly from the reservoir, and the compressor is activated to restore the pressure of the reservoir.
The valve block regulates airflow to control the inflation and deflation of the air springs, ensuring that each air spring receives the correct amount of air, based on input from the ECU.
When excess pressure needs to be released, air flows back from the air springs to the valve block, where it is either expelled through a pressure-release valve or stored in a pressure reservoir for later use.
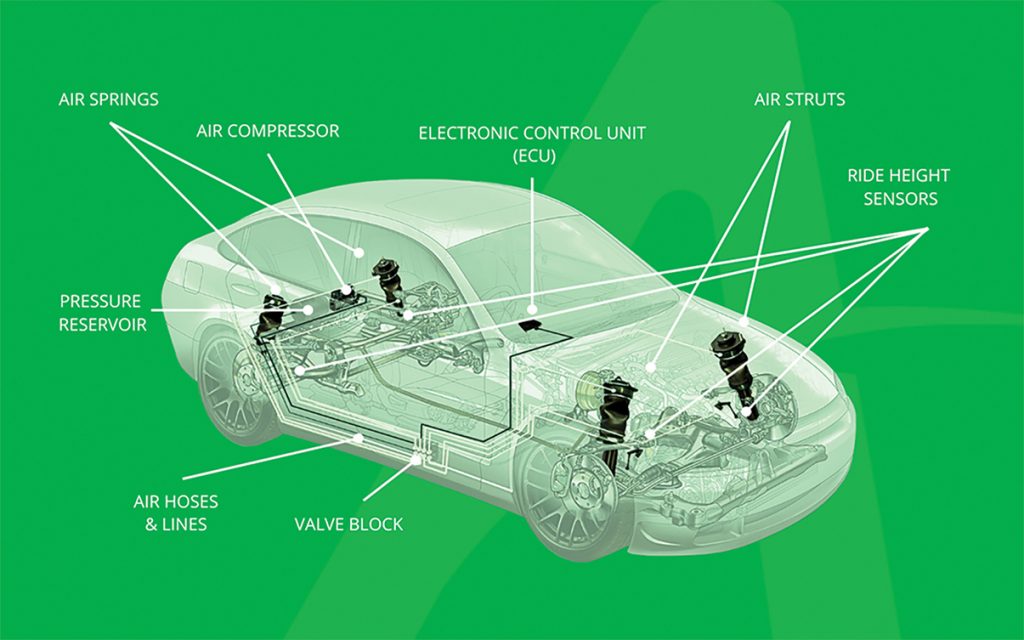
The pressure reservoir, typically positioned towards the rear of the vehicle, acts as a buffer and storage unit for compressed air.
Maintaining a reserve of pressurised air allows for rapid height adjustments while reducing the frequency of compressor activation.
This minimises wear and overheating of the compressor, helping extend the system’s lifespan and improving overall efficiency.
The ECU serves as the brain of the air suspension system. It processes data from height sensors while monitoring engine speed, acceleration, and system pressure to determine whether the air springs need to be inflated or deflated to achieve the predetermined ride height.
The ECU accomplishes this by regulating the solenoid valves within the valve block and activating the compressor to supply the necessary air pressure, ensuring that the suspension dynamically adapts to changing driving conditions.
A common misconception is that the air suspension system continuously inflates or deflates the air springs to adjust for every movement, such as during cornering.
In reality, advanced suspension systems incorporate electronically controlled shock absorbers that instantly adjust stiffness.
These absorbers adapt to driving conditions, stabilising the vehicle during turns, braking, or acceleration without the need for constant air adjustments.
Arnott says this results in a more responsive and efficient system that maintains a smooth and controlled ride.
Mounted between the axle and the chassis – typically at each corner of the vehicle – ride height sensors continuously monitor the vehicle’s position and ride height, transmitting this data to the ECU.
When a deviation from the preset ride height is detected, the ECU evaluates whether adjustments are needed. If so, it signals the valve block to implement the pre-calculated height adjustments.
This automated cycle ensures that the suspension system promptly adapts to fluctuations in weight, road conditions, and driving dynamics.
All components of the air suspension system work seamlessly to deliver a controlled, adaptive, and comfortable driving experience.
While air suspension shares some similarities with traditional suspension systems, air suspension stands out with several distinct advantages including adjustable ride height, enhanced comfort and reduced NVH, automatic load-leveling, and improved stability and fuel efficiency.
For more information, visit www.arnottinc.com