CNC MACHINED TANKS
Not just pretty machined faces
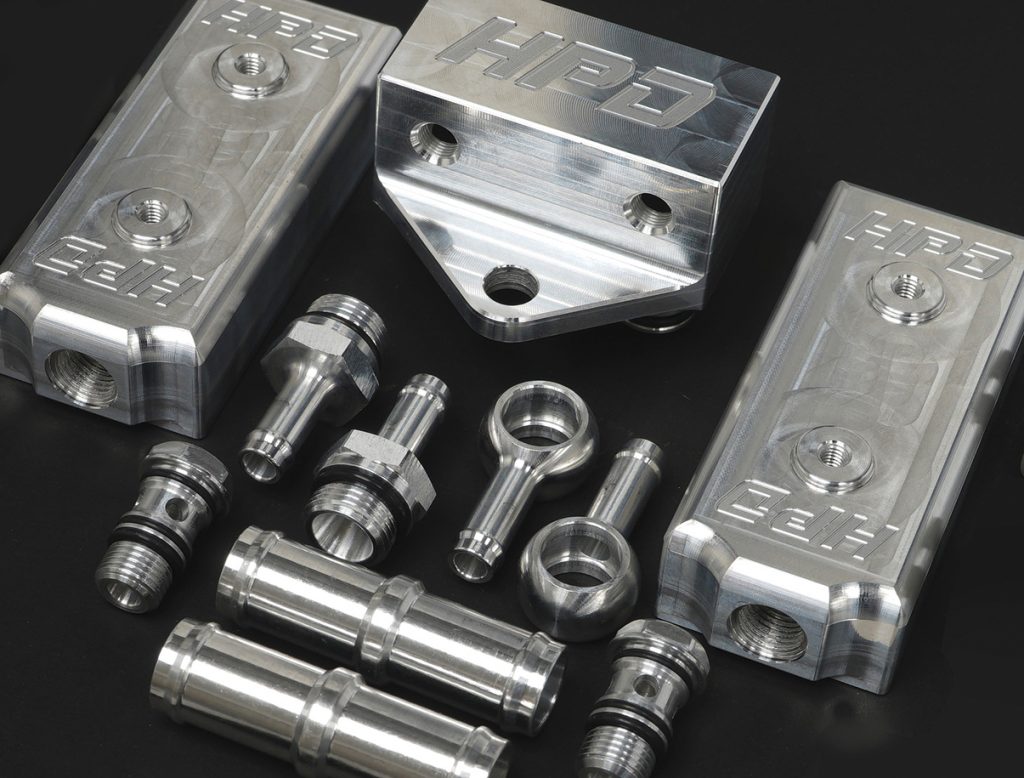
High Performance Diesel (HPD) has recently made a significant investment in its fourth state-of-the-art, automated five axis CNC machine.
Even though modern multi-axis CNC machines make producing parts easier and faster than ever, it still requires years of engineering, machining and programming experience to deliver highly functional, premium quality parts.
HPD utilises multi-axis CNC machines to produce over 350 different part numbers which include components ranging from small fittings to the impressive adapters, catch cans and cooler tanks that HPD are famous for.
HPD says most people are surprised when they discover that it goes to all the effort and expense of producing its own, seemingly insignificant fittings and joiners, stating it is a testament to its obsession with quality.
HPD says the apparent ease of placing a block of billet alloy into a modern CNC machine, then removing a finished part is obvious, but posits, what are the benefits to the end user?
Are there advantages to fitting intercoolers and oil coolers with tanks machined from solid billet alloy?
HPD explains the benefits are as follows.
Go with the flow
With the aid of CAD, tanks can be designed to optimise flow. This is a significant advantage particularly for intercoolers, where parameters like improving flow and distributing air evenly over the width of the core can be utilised to improve performance and minimise hot spots.
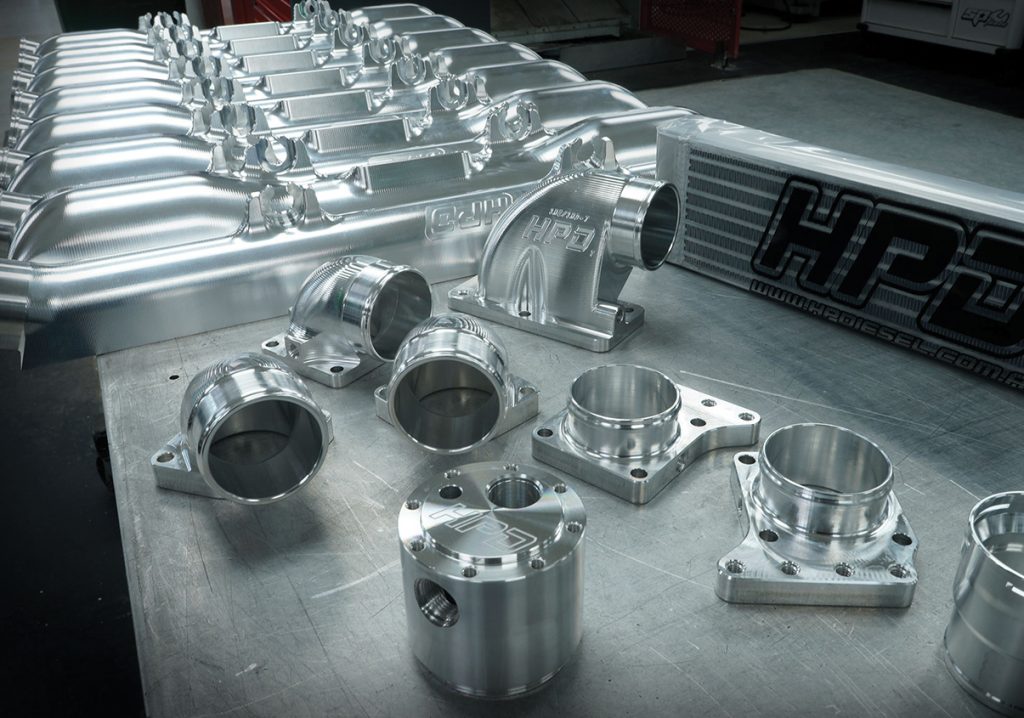
Consistent and resistant
Arguably the most important benefit is consistency. Parts can be reproduced to a consistent high quality, ensuring all components in the kit (such as fans and switches) can be assembled accurately and ultimately fit correctly to the vehicle.
Compared to pressed or hand fabricated tanks, areas of potential weakness, for example, around sharp curves, folds or welds can be eliminated.
With full control over material thickness, CNC machined tanks have virtually no failure points (if designed correctly).
This is a huge advantage for parts that need to operate under pressure, like oil coolers and intercoolers.
As HPD parts are designed mainly for four-wheel drive vehicles that perform off-road driving, CNC machined parts can be easily manufactured to be extremely durable, resisting sustained vibration, impact from debris and sudden body movement that drivers experience on rough outback terrain.
The bling factor
Last but certainly not least, for some, the main benefit is the smile you get when you lift the bonnet and enjoy the jewel-like shine of machined billet alloy parts.
HPD says it takes immense pride in the appearance and quality of its products.
Waste not, want not
HPD says an interesting fact is that it delivers more than three tonnes of Aluminium swarf every month for recycling.
Further, it says that impressively, approximately 80 percent of the coolant (required to keep the cutting tools lubricated) is also recovered and recirculated.
For more information, visit www.hpdiesel.com.au