DRIVING TOWARDS A GREENER FUTURE WITH INFINITEV
Extending the useful life of products not only saves the environment, but can also be good for business
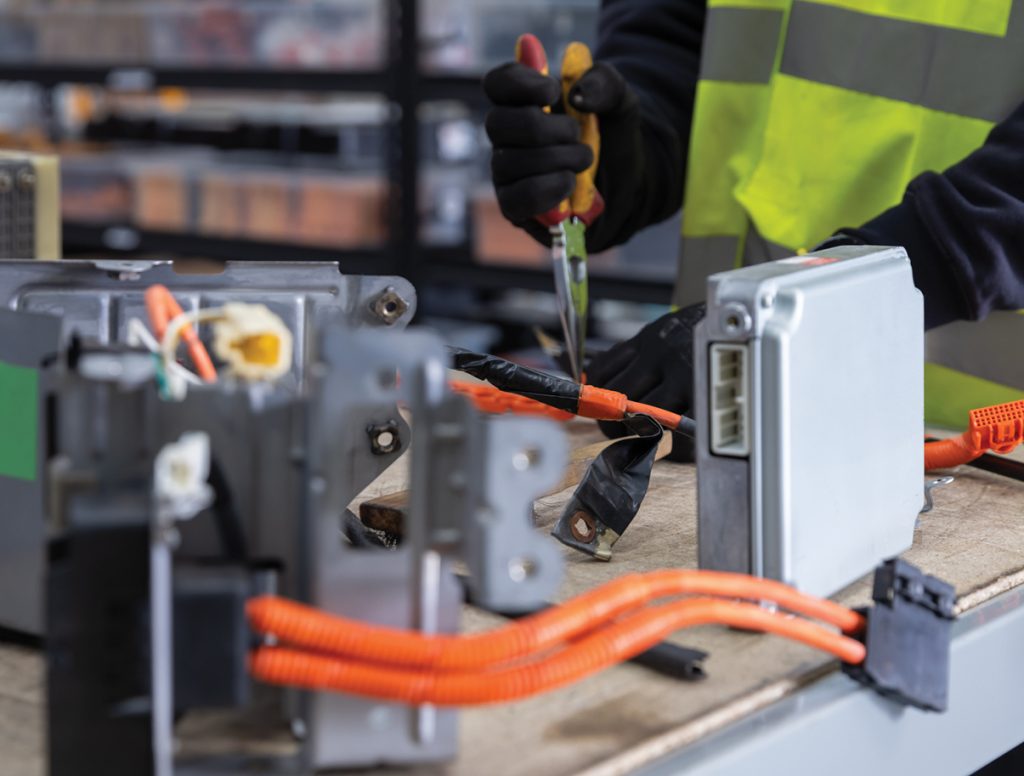
As the automotive industry increasingly prioritises sustainability, Infinitev says it stands out with its innovative approach to remanufacturing hybrid and electric vehicle (EV) batteries.
By extending the life of existing batteries, Infinitev explains it significantly reduces the demand for new raw materials, lowering the overall carbon footprint associated with battery production.
The importance of this approach is underscored by a comprehensive lifecycle analysis conducted by the University of Melbourne.
The study shows that replacing a Toyota Camry 50 series battery with a genuine new one incurs 1,256 kg of CO2-equivalent (CO2e) emissions. By contrast, one of Infinitev’s rebuilt batteries reportedly has a footprint of only 18 kg CO2e: a saving of more than 98 percent.
“It helps that we have a roof lined with solar panels and microgrid to power our operations, and everything else we need to build our batteries is remanufactured components and our battery engineers,” Infinitev Executive General Manager, Bart Moonen, said.
“We’ve set up Infinitev as a circular economy business – we’re here to show that extending the useful life of products not only saves the environment, but also that it can be good for business and for customers.
“One of our remanufactured batteries will be anywhere between twenty and fifty percent cheaper than genuine, and is backed by a three year warranty.
“It is the difference between keeping the car on the road and looking for a new one for many customers.”
Infinitev says its commitment to sustainability extends beyond remanufacturing.
The company has developed reusable transport cases, addressing the challenge of transporting batteries efficiently.
These durable cases minimise waste and reduce the need for single-use packaging materials.
“It makes life easier for the automotive workshops too,” Bart said.
“We ship new packs to the technician, they swap it for the faulty one and ship the old back to us in the same case.
“They’re not stuck with a bad battery taking up space in the workshop.”
Once back at Infinitev’s facilities, the batteries are tested for remanufacturability: good parts are used to rebuild batteries, and bad parts are processed to recover the raw materials so that they can be used to make new batteries.
Infinitev says this closes the loop for a circular system that’s good for the environment, and good for business.
For more information, call 1300 360 111 or email hello@infinitev.au