HYBRID MODEL BOOSTS BENDIX’S LOCAL MANUFACTURING
Bendix says it is the last remaining aftermarket automotive brake manufacturer in Australia
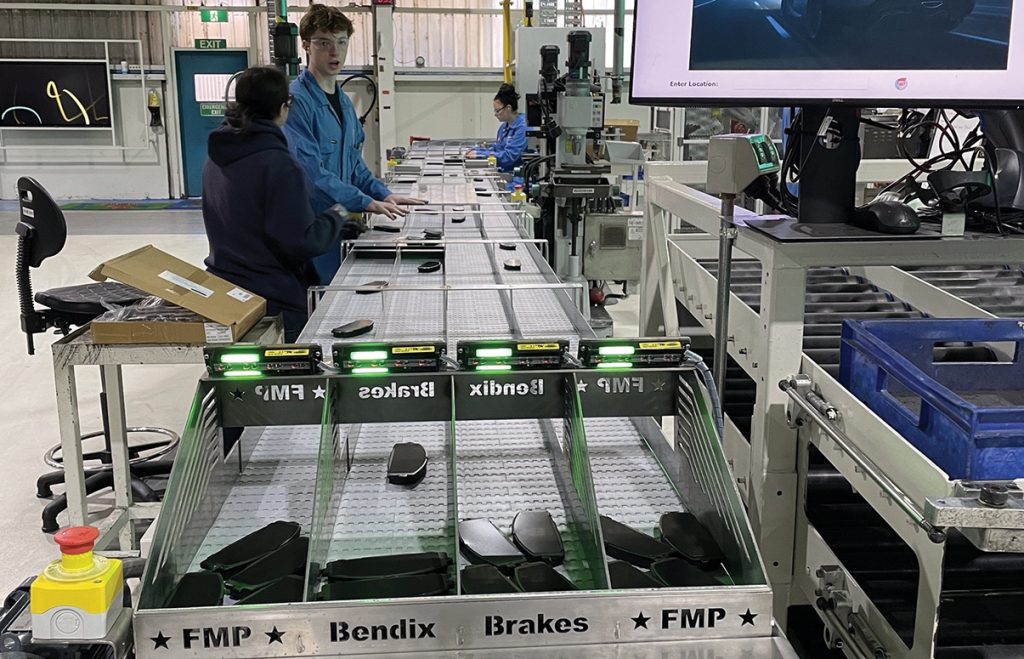
Bendix develops a wide range of disc brake pads from its Ballarat facility which are locally designed, engineered and made for Australia’s demanding conditions.
As well as servicing the domestic market, Bendix exports selected disc brake pads to New Zealand and much further afield, including to the Middle East.
Bendix explains that it is the company’s hybrid manufacturing capabilities that let it stay competitive, while stimulating technological advancements and new processes.
Bendix says its two-pronged approach to manufacturing centers on its ability to handle both low and high volume manufacturing runs depending on customer requirements.
Bendix also states its local manufacturing presence also means that the company can turn around orders – from manufacture to stock on shelves – much faster than competitors who are affected by long import supply chains.
High volume manufacturing runs for popular vehicles
The bulk of Bendix’s high volume runs are handled with its semiautonomous press, which has the capacity to manufacture as many as 2,000 disc brake pads per shift or 4,500 over a full 24 hour production cycle.
The clever machine is computer controlled and loads friction material mixes into its four cavity mould dies itself, before using a 160 tonne press to compress materials into the required shape and consistency.
The unit is able to manufacture up to six different pad types (for different model cars) at once, and can also handle a variety of pad types (General CT, 4WD/SUV etc) at the same time. Importantly, Bendix says production errors using this machine are virtually nonexistent.
The cavity moulds for each different brake pad model are designed and engineered in-house by Bendix engineers, ensuring they meet the company’s stringent quality control requirements.
The semiautonomous press is currently being kept busy producing disc brake pads for high selling local Ford Ranger and Toyota Hilux models, and Toyota Camry MVP (dealer bought parts) / OES (Original Equipment Supplier) pads that are being supplied to Toyota for export to the Middle East.
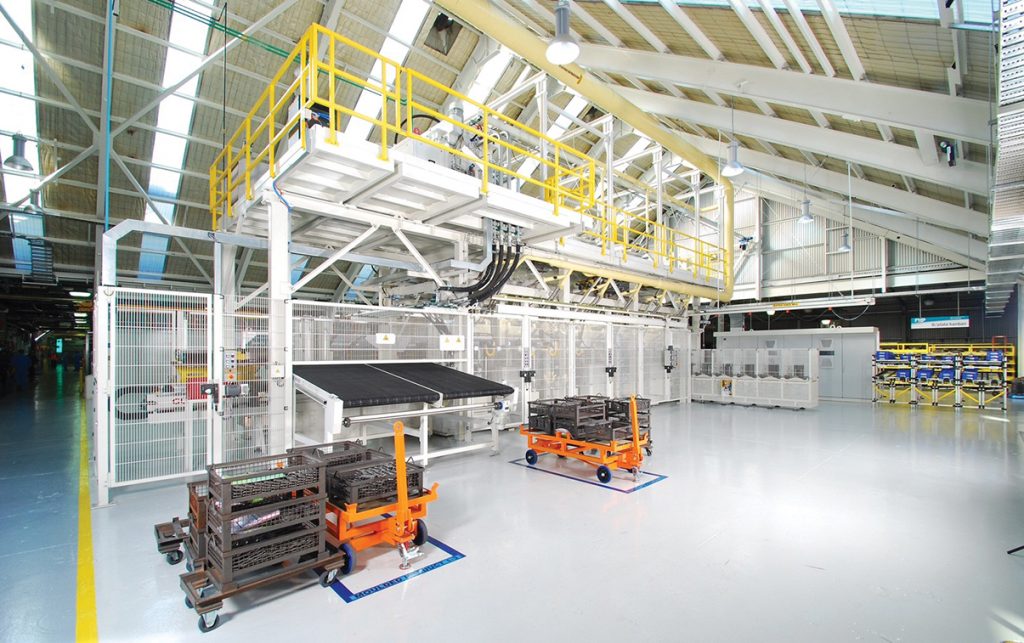
Fast and nimble short run production
Smaller volume production at Bendix’s manufacturing facility is handled manually by production staff on machines known as ‘Troika presses.’
The Troika presses were designed and built in Ballarat along with their cavity moulds. Each production team member typically oversees four Troiker presses in rotation across two shifts to minimise repetitive processes; per shift, these presses typically produce around 300 brake pads.
Within this timeframe, the team can manufacture pads to suit between 15 and 20 different models, this means that the brake pads can get to market quickly and efficiently. From the time of order to stock at the warehouse is normally less than a week, says Bendix.
Bendix also states it is well progressed in further increasing its short run capabilities working towards being able to efficiently produce single, made-to-order products, which will be a gamechanger for the industry.
Streamlined production
Away from the presses, Bendix has also recently introduced line changes that bring greater efficiency to the packaging process of its disc brake pads.
Advanced new scanning and sorting methods means that disc brake pads can be finished together in complete sets.
Previously, different brake pad components needed to be picked and brought together for batching and packaging.
The new process sees the brake pads ground, painted and branded ‘left’ and ‘right’; shims and abutment clips are then added on the line, and together the complete pad set is ready for shrink wrapping and boxing at the same time.
Bendix says these line upgrades have reduced line set-up time by 30 minutes per day, while also increasing the number of finished pieces per shift from 6,500 to approximately 8,000 pieces.
For more information, visit www.bendix.com.au