LIQUI MOLY INVESTS EIGHT MILLION EURO IN THE EXPANSION OF ITS PRODUCTION IN ULM
Three new additive dispensing systems increase maximum output capacity by 40 percent
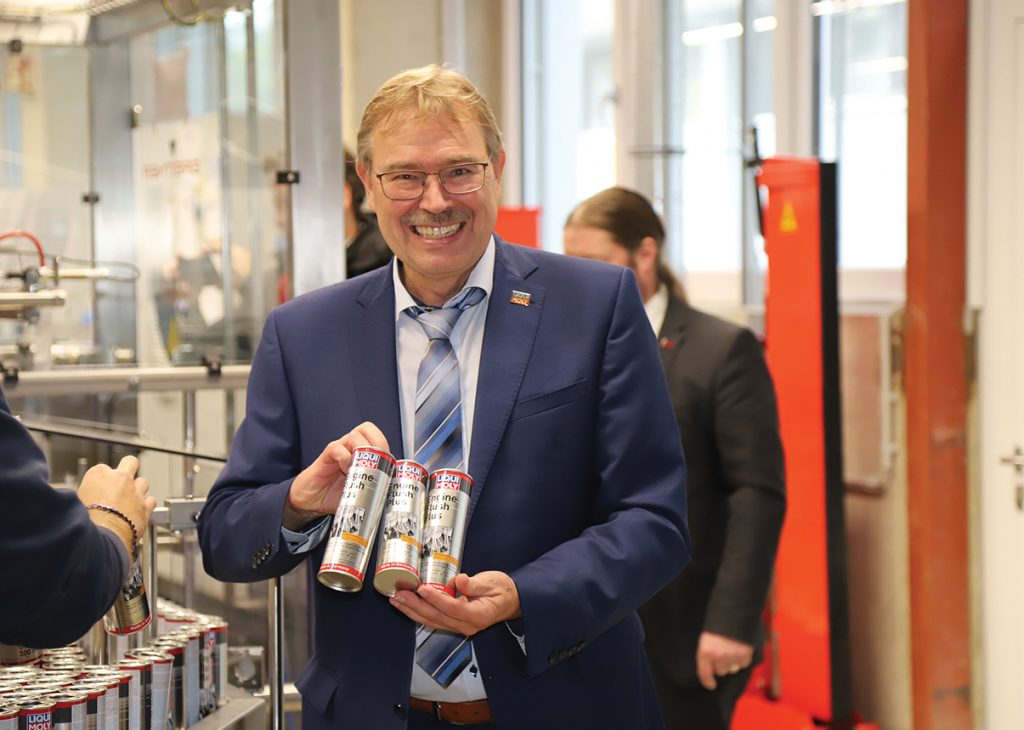
Liqui Moly is opening a new chapter at its headquarters in Ulm: Managing Directors Günter Hiermaier and Dr. Uli Weller have inaugurated the new building for the production of additives with three modern dispensing systems and additional office space.
The new machines increase the maximum output from 346,000 cans per week to up to 481,000.
“The kick-off marks a milestone on our way to achieving our joint sales target of 1 billion euro,” the pair said in front of representatives from politics, business, the media and the workforce.
Liqui Moly has invested eight million euro in the newly opened additive production facility.
Of these, 3.4 million euro are attributable to the turnkey building. The costs for the three new dispensing systems amount to 3.1 million euro. Conveyor technology and packaging robots account for 1.4 million euro.
These machines will be fully installed and commissioned over the course of 2024.
Liqui Moly explains that additives help engines to burn fuel cleanly, emit less pollutants and have a longer service life. They can be used as a preventative or problem solver.
Liqui Moly develops and manufactures all of its additives in Ulm.
“These investments are a commitment to the Ulm site and thus to Made in Germany. We create more jobs and give people a long-term perspective,” Günter said.
Of course, the machines have an impact on the employees, but contrary to what may be assumed, Liqui Moly says new machines do not mean fewer people, but a growth in jobs in other areas as well, because more is produced.
Further, it says working conditions will continue to improve.
“Liqui Moly is a modern employer. People should and must feel comfortable working here with us. This is what we demand of ourselves,” Günter said.
“That’s why 200 square meters of space were created for state-of-the-art offices on the third floor, in addition to the 400 square meters of production space spread over two floors.”
The conditions during the construction phase were less pleasant. The production building between the existing production and the administration building was constructed during ongoing operation.
Under difficult circumstances, the employees in work preparation and production kept the company running at full speed.
“That’s why I would like to express my special thanks to them and all those responsible for the project,” Günter said.
The Liqui Moly Managing Director also thanked Jörg Murawski, Managing Director of Würth Elektronik and Executive Vice President of the Würth Group, to which Liqui Moly has belonged since the beginning of 2018.
“Würth gave us free rein in all decisions, and at the same time security and also a lot of know-how. Würth supported us in all phases of the project, and strengthens us with profitable cooperation and trust in our chosen path,” Günter said.
To learn more about Liqui Moly, visit www.liqui-moly.de or www.liqui-moly.com.au