PRODUCTS TESTED FOR SUCCESS
MAHA Australia has been servicing the aftermarket industry since the early 1980s
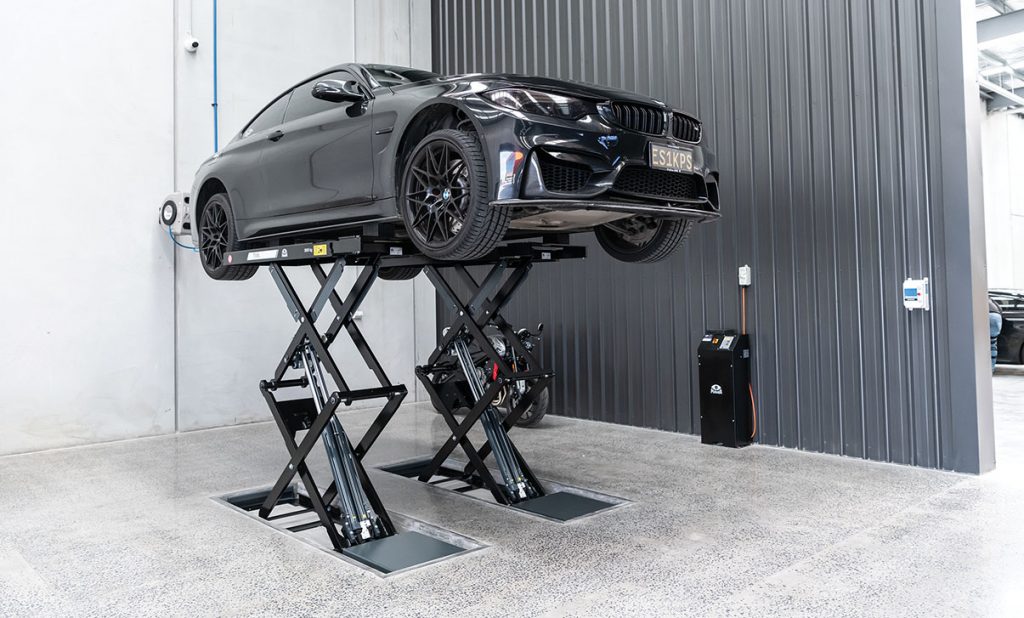
MAHA has been manufacturing high quality, specialised workshop equipment for over 50 years and says it is renowned worldwide for being a leader in brake testing technology.
The company supplies products that cover various inspection devices for cars, trucks, motorcycles, and special-purpose vehicles.
With the option of linking individual test devices to form universal test lanes, MAHA states it has become a skilled technical partner for clients all over the world.
MAHA asserts that its products meet the highest quality standards, representing reliability and long service life while satisfying the most demanding requirements.
“MAHA Australia has a long history of outstanding customer service being ISO 9001:2015 quality management system certified for 31 years running,” MAHA Managing Director, Mick Lauster, said.
“Our success in Australia rests on our ability to control the complete supply chain from manufacturing in Germany right through to delivery, install and across the service life of its product.
“With an extensive range of spare parts and standard MAHA products in stock, we can also supply urgent spare parts for maintenance and installations of MAHA products.
“Our equipment is used in facilities all around Australia, New Zealand and now the Pacific Islands with many new sites enjoying the speed and safety of our rising bed load simulation.
“The strong relationships we have with both Inspection-based and private customers are due to the unique fact that we are a brake and suspension testing-equipment supplier that can manufacture, supply, install, repair and calibrate our equipment, which is a good reason for most serious clients to give fair consideration for this equipment.”
The types of equipment MAHA can install into a dealership, workshop or testing facility includes but is not limited to brake, weight, and suspension testing equipment; the MAHA 18T Roller Brake Tester for dynamic brake testing and gross weight; the MAHA Rising Bed option for dynamic load simulation; and the MAHA 20T Axle Play Detector.
MAHA says potential customers can be confident the company will support them throughout the whole process, from planning the workshop layout and conducting the civil works, including concrete cut plus pour, to installation, training and on-going support from an extended sales and support process.
MAHA’s Civil installation process is completed with the full support of the customer and completed within a week by MAHA technicians, who are able to streamline planning, civil works, electrical and coordinate the whole process for a time-efficient professional outcome.
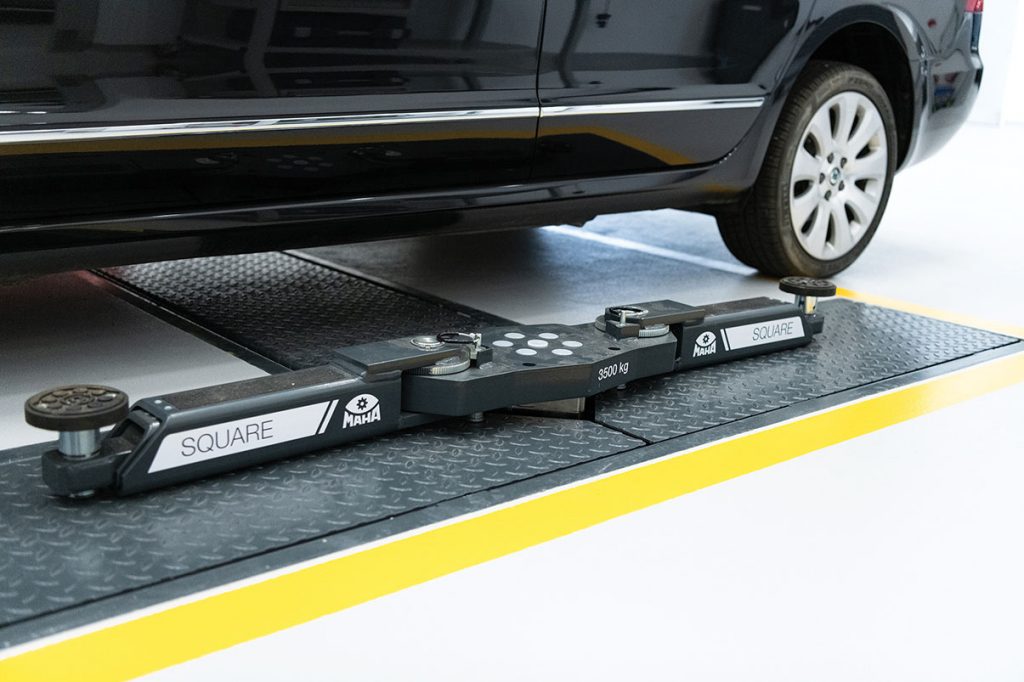
Brake, weight and suspension testing equipment
New testing facilities are supplied complete with a drive-on/drive-off system for high volume testing with iPad operation for the inspector.
Using these systems, wheels are rolled at three kilometers per hour while the drag, brake force, load simulation, imbalance and gross weight are all checked in the same process.
The vehicle is then parked with the axle on the suspension tester while the inspector views for defects underneath. MAHA says the benefits and advantages of this testing process include:
• Time efficiency, offering easy access to a mandatory testing system
• Speed and safety during load simulation
• Accuracy
• Repeatability
• Dependability
• Minimal staffing requirement for hassle-free operation
MAHA says it has hundreds of satisfied customers that have experienced decades of fault free operation, maximum reliability and consistency of readings, and states these unfailing results have kept operations running smoothly, avoided costly downtime and generated optimum performance for clients around the country.
“We are particularly proud to show new customers our existing sites because it showcases the standard and quality of the German engineering behind the MAHA brand,” Mick said.
“Some units have been in service for over 25 years and are still as accurate and reliable as the day they were in installed.
“This is partly due to the German manufacturer’s build quality, but also because we utilise our in-house team of factory trained technicians to service and calibrate all machines and support clients across the country. This is unique to the Australian market and is what sets MAHA apart from our competitors.”
MAHA 3.5T to 18T Roller Brake Tester
When it comes to the MAHA Roller Brake Testers, they are available in 3.5 Tonne, 15T and 18T “Axle” capacity and offer the following features:
• Roller Brake Tester speed three to five km/h, this does not engage ABS systems but allows a full rotation of the testing wheels to obtain the most accurate and repeatable test results
• Includes drag detection – for example, wheel bearing or sticky caliper piston
• Includes warped rotor or oval drum test
• Optional license plate recognition
• Static and dynamic Gross Vehicle Weight
• Front and rear brake force and park brake test
• Electric park brake or air park brake test
• 4WD mode – an original MAHA Patented feature
• Bi-directional testing
• Electronic, temperature-compensated strain gauge system for highly precise measurement results under all environmental conditions for repeatable and accurate readings.
MAHA’s system doesn’t just provide a “Pass/Fail” Brake test result. MAHA says users are also able to comprehensively diagnose faults with the Brake system without removing the wheels, providing maximum accuracy and allowing for faster throughput in the workshop.
MA Star Two-Post Lift
MAHA has brought to Australia the German-made MA Star two-post lift, which has a 3500kg load capacity.
It has a triple safety feature and a 20-year plus proven spindle-nut system with self-locking thread and comes with a five-year warranty.
The MA Star two-post lift comes in several models: the MA Star 3.5A Asymmetrical and MA Star 3.5S Symmetrical and a now available 5500kg load capacity version.
The MA Star 3.5A includes asymmetrical columns turned by 45 degrees for a generous door-opening angle, and asymmetrical support arms. The support arms have a 180-degree range. The optional MA Star 3.5S comes with symmetrical columns for a reduced overall width and symmetrical support arms.
The MA Star 5.5 has been designed to accommodate larger vehicles and long wheelbase vans and is now available from stock.
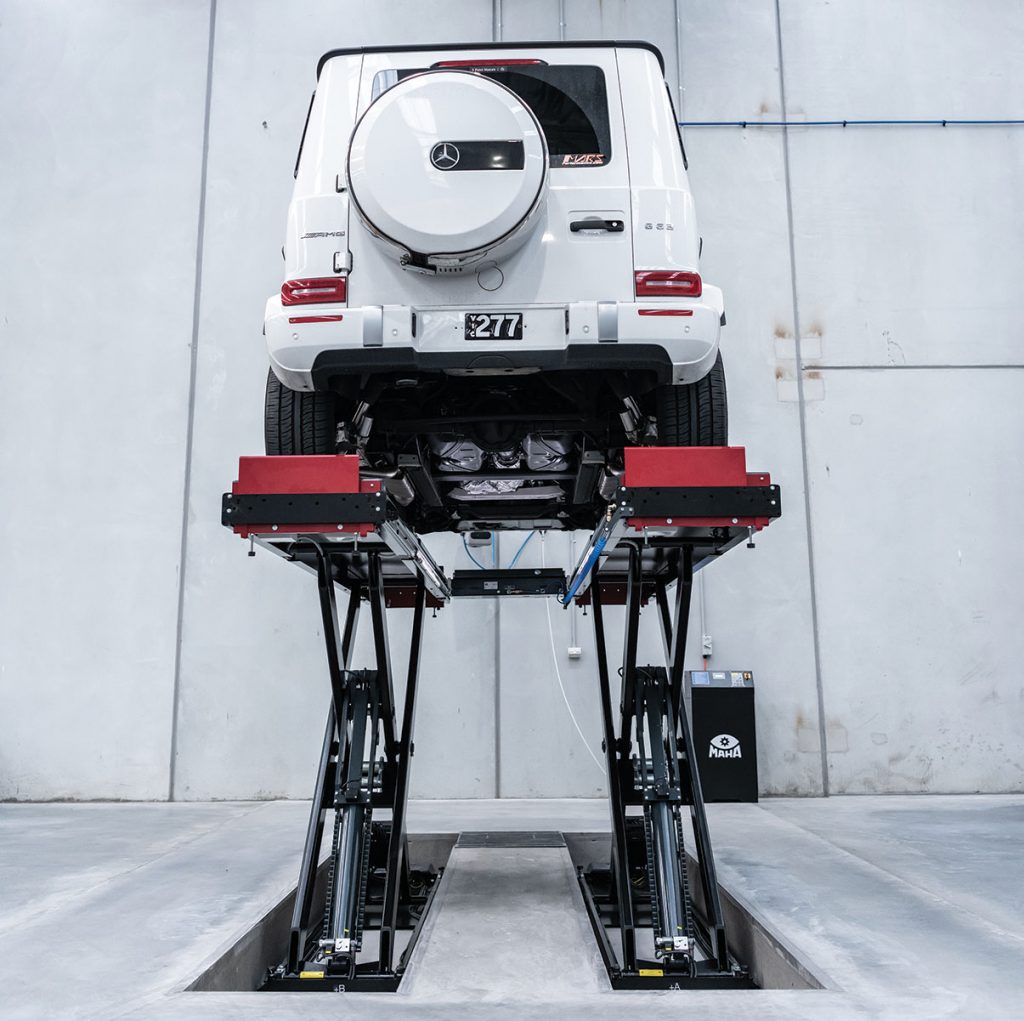
The customer can choose from numerous additional options, including the LED lighting kit or the 5.5 specific wheel fork supports for special and electric vehicles, which allow unrestricted access to the underside of the vehicle and thus facilitate the removal and installation of vehicle batteries. These supports are also ideal for municipal vehicles such as street sweepers, which often do not have mounting points for support arms.
All models are available with variable installation width and are finished with your choice of powder coating or are supplied in standard RAL 7040 window grey on the columns and RAL 7016 anthracite grey on the support arms.
The lifts boast the following features as part of standard delivery:
• Two asymmetrical columns with control panel at operating column
• Four asymmetrical support arms
• 80mm standard pick up pad height suitable for lowered vehicles (MA STAR 3.5 only).
• 50mm and 100mm extensions that can be combined to achieve 150mm for large side steps
• Adjustable Cable bridge for low ceiling installation
MAHA lifts are manufactured in Bavaria in Germany and hold Factory approvals with the German OEMs. These approvals are only obtained by adhering to strict lift requirements across the entire range, says MAHA.
The features of the MA Star 3.5A and MA Star 3.5S are further highlighted in a YouTube video, which can be found on the MAHA Australia and New Zealand YouTube Channel.
For more information, please contact the team at MAHA Australia on 1800 006 242 or visit www.maha.com.au