ZF AFTERMARKET SOLUTIONS FOR A SUSTAINABLE AUTOMOTIVE AFTERMARKET
ZF presented two remanufacturing initiatives at Automechanika Frankfurt
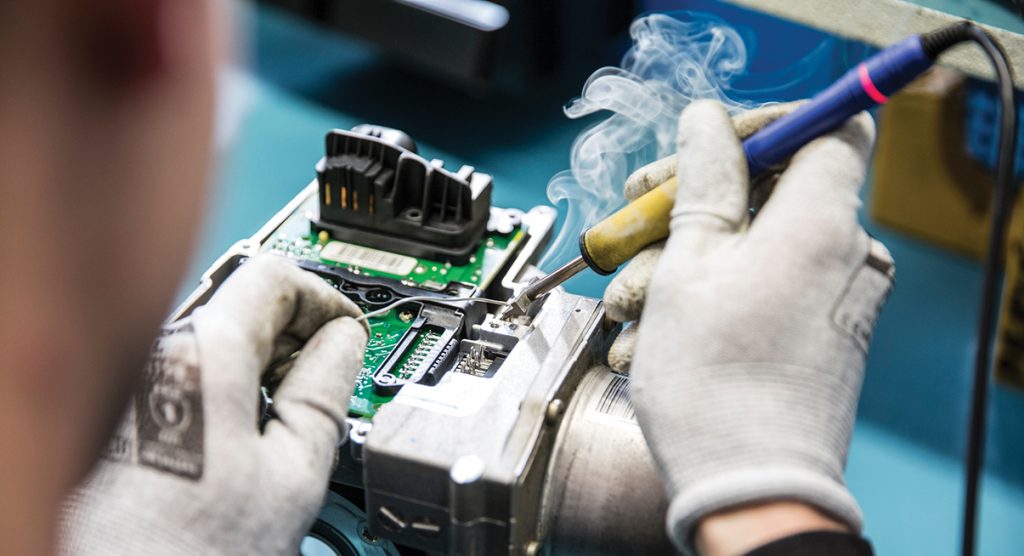
With the remanufacturing of used vehicle parts conserving resources and avoiding CO2 emissions compared to the production of new parts, ZF says it forms an essential part of its sustainability strategy.
With the new ZF REMAN label, ZF Aftermarket explains it has increased remanufactured product visibility across all its premium brands.
As the return of used parts is the decisive cornerstone for remanufacturing, ZF Aftermarket says it has also optimised a customer-friendly process for reverse logistics, ‘CorExpedia.’
ZF Aftermarket presented both solutions at Automechanika Frankfurt 2024.
ZF REMAN products
ZF Aftermarket says the new ZF REMAN label reflects the increasing importance of sustainability for customers across the automotive aftermarket.
It says sitting behind this are industrial remanufacturing processes, which take place at ZF’s own plants worldwide to guarantee the same quality and functionality of new parts, but with avoided raw material consumption along the supply chain.
ZF Aftermarket says every remanufactured part undergoes tests and checks to ensure that it fulfils the same requirements and has the functionality of a new part.
The parts are not just cleaned and repaired, but are brought up to the current series standard; an industrial production standard.
ZF says its factories, ISO and IATF certified, bring the OE heritage and know-how to the reman facilities, where worn single elements are replaced and, if necessary, improved components are retrofitted to increase performance and service life.
The warranty period for ZF REMAN parts is identical to that for new parts or even longer, with ZF Aftermarket stating this gives workshops and end customers the certainty that they can rely on ZF REMAN parts in the same way as on new parts.
CorExpedia: an internet-based return platform for used parts
The basis for remanufacturing is the return of used parts (cores) from workshops via wholesalers to the manufacturer.
This so-called reverse logistics process must be as simple, fast, and as efficient as possible so that garages and distributors can easily use it.
ZF Aftermarket’s solution to meet these challenges is CorExpedia, which it explains is an intuitive and user-friendly online platform for returning cores globally.
Initially devised for returning WABCO branded parts in Europe, ZF Aftermarket says CorExpedia has already been proven to significantly improve return efficiency.
It states the tool is easy to use, and the process very fast, for example when it comes to deposit refunds. And now, ZF Aftermarket is gradually rolling out the concept to its entire portfolio.
With the wider launch this year, selected SACHS-branded used parts can be returned via CorExpedia, for the first time.
The portal can be used on any internet-enabled device and only a few clicks are required to organise a return.
Clear user instructions can be found in the CorExpedia portal, including return guidelines and specified details about part return condition; and practical analysis functions of the portal make it possible to monitor the status of returns and create reports.
There is also clear information on deposit refunds. Of particular note, the functionality known as the ‘core bank’ clearly shows the number of parts purchased from the returned cores and enables users to determine at a glance whether they have already exhausted their return potential.
“With ZF REMAN and CorExpedia, we want to offer customers even easier access to our remanufactured products,” ZF Aftermarket Head of Remanufacturing Strategy and Business Development, Tomasz Galazka, said.
“Our goal is to continuously expand our remanufactured parts portfolio contributing more significantly to resource conservation and emission reduction.”
For further information on ZF in Oceania, please visit www.zf.com/au